New Construction
Spray Foam Insulation for new homes
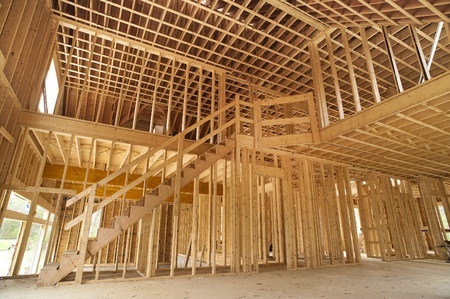
An important measure of home comfort is how occupants feel on a daily basis – and how much they spend on heating or cooling. A home that keeps occupants cool in summer and warm in winter is just one important feature to prospective homebuyers.
Production Homes
Air sealing your production homes with AEI spray foam insulation creates a protective barrier that
dramatically impacts home comfort in ways conventional insulation like fiberglass and cellulose cannot.
Your clients deserve to live comfortably and you can provide them a home that provides that as well as a healthy environment.
Combining production built homes and spray foam insulation is not as costly as you may think. AEI has narrowed the price gap between spray foam and other insulation types. Work with AEI to get a whole house cost analysis to understand how affordable spray foam really is. Spray foam in your construction projects provides you with many off sets that add up to great savings. AEI will evaluate your homes building envelope to help you realize cost savings from products that are downsized or eliminated with spray foam insulation.
Lower Construction Costs / Builder Advantages
With spray foam, you can lower construction costs, meet or exceed today's stringent building code requirements, and provide your customers with the benefits of spray foam.
Benefits to likely lower construction costs:
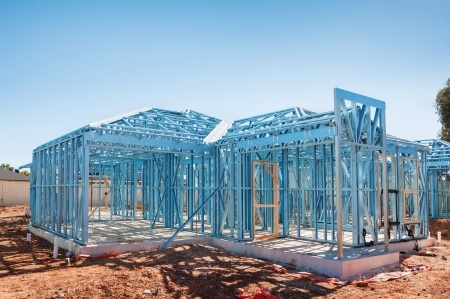
- by reducing the amount of added air sealing required to meet code requirements. Spray foam acts as both insulation and an air barrier that seals the building envelope, reducing the need for additional air sealant materials. Also, some jurisdictions require air tightness tests to prove compliance. A spray foam building assembly can be tested before the drywall is applied, which could save you time and avoid costly repairs if defects are found.
- by reducing construction time. Spray foam fits into hard to reach places and can be applied directly onto existing roof coverings, which could eliminate the need for costly and time consuming tear-off and replacement.
- by taking advantage of tax incentives. Spray foam may qualify you for tax credits and incentives.
Meet or Exceed Building Code Requirements:
- States and localities continue to adopt codes that encourage or mandate increased energy efficiency. Spray foam roofs and insulation can help you meet or exceed stringent building and energy codes.
- Builders participating in programs such as Energy Star, LEED, and NAHB Green Building Certification may qualify for streamlined inspections and reduced fees. Spray foam can help you meet the energy efficiency requirements of each of these programs, potentially eliminating the need for a local code official inspection of energy elements.
Provide Your Customers with the Benefits of Spray Foam
Whether it's a home or office building, strip mall or corner store, owners are concerned about building performance and energy efficiency. Spray foam can help you provide long-term value to your customer. With spray foam, your customers can enjoy many benefits like energy efficiency, durability, low maintenance, leak-resistance, wind protection, and comfortable, draft-free homes or buildings.
Understand the advantages of Spray Foam Insulation in Custom Built Homes
While your clients may have heard about spray foam, they may not realize the advantages of spray foam insulation in custom built homes. When building a new home, it's the best time to have spray foam installed. Homeowners are typically ahead of the curve in pursing energy efficient solutions for their home. Spray foam not only addresses a key concern for homeowners but can noticeably reduce their monthly heating and cooling costs.
With spray foam, you can insulate hard-to-regulate temperature zones such as basements, crawl spaces, bonus rooms and attics. Your clients will never have to experience cold floors again! Exceed your client's expectations on comfort by building them the home of their dreams with a comfort level beyond their imagination, only delivered with spray foam.
So, why use spray foam insulation in custom built homes? To provide your clients with continual comfort, energy efficiency and significant monthly savings. The comfort they will experience will reinforce to homeowners the quality their builder has put into their home and the excellence of the builder they have chosen.